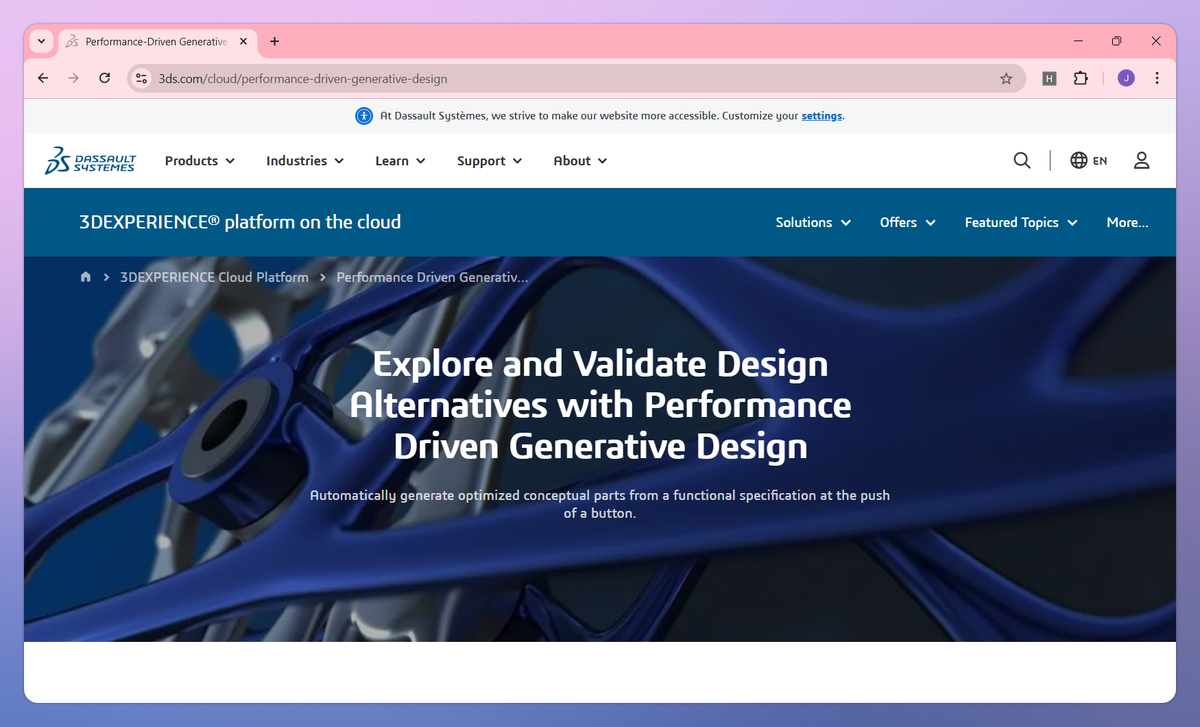
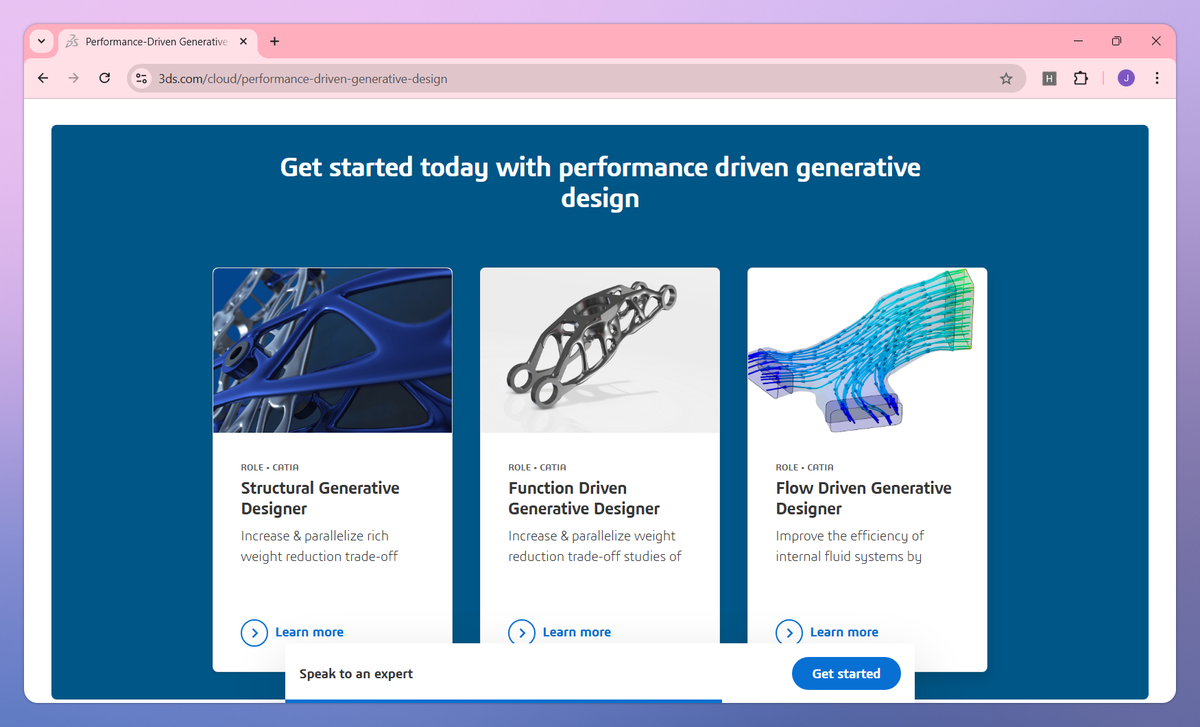
What is Performance Driven Generative Design?
Performance Driven Generative Design is an AI design tool that automatically creates optimized part designs based on functional specifications and performance requirements. It generates structurally validated shapes that reduce weight and meet performance targets, allowing engineers and product designers to explore multiple design alternatives without simulation expertise.
What sets Performance Driven Generative Design apart?
Performance Driven Generative Design sets itself apart with specialized design modes for both structural and fluid flow optimization, giving mechanical engineers freedom to create shapes that would be impossible with traditional design methods. This multi-variant approach proves valuable for design teams who need to make data-driven decisions when comparing different design concepts and their key performance indicators. The system's built-in understanding of manufacturing constraints for both additive and traditional methods like milling, casting, and forging allows product teams to move directly from concept to production without rework.
Performance Driven Generative Design Use Cases
- Automated concept generation
- Structural design optimization
- Weight reduction simulation
- Fluid flow optimization
Who uses Performance Driven Generative Design?
Features and Benefits
- Generate optimized conceptual parts automatically from functional specifications at the push of a button, creating designs that conventional methods cannot achieve.
Automated Concept Generation
- Explore and validate design alternatives through integrated simulation, making informed decisions on weight reduction and performance optimization.
Performance Simulation
- Set up and run generative design cycles without simulation expertise, creating lightweight components with significant performance improvements.
Accessible for Non-Experts
- Design with specific manufacturing constraints from the start, including support for additive manufacturing, milling, casting, and forging processes.
Manufacturing Process Integration
- Improve internal fluid systems efficiency through automatically generated shapes that minimize pressure drops and maintain mass flow rates.
Fluid Flow Optimization
Performance Driven Generative Design Pros and Cons
Creates exceptionally realistic and high-quality 3D renderings
Powerful modeling tools with extensive customization options
Excellent for architectural visualization and interior design projects
Streamlines collaboration between different design disciplines
Requires significant computer processing power and memory to run effectively
Steep learning curve with complex interface that takes time to master
Very long render times for high-quality output
Expensive licensing costs compared to alternatives